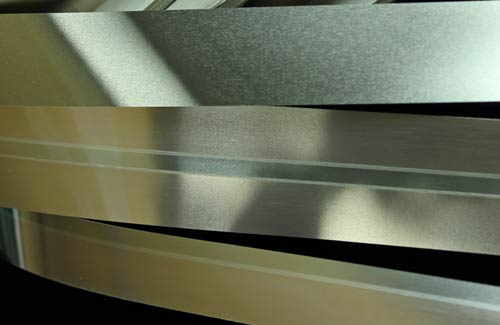
Deringer-Ney has developed a bimetallic strip to enable customers to thrift precious metals in electrical contact systems and utilize lower cost conductive materials where precious metals are not needed. Bimetallic strip allows engineers to design in precious metal at the point of electrical contact, while using a non-precious alloy for the rest of the component.
Each bimetallic strip is designed to meet component and application requirements. A common bimetallic material combination is Paliney 6 (a palladium alloy) and a spinodal alloy like C729, which contains copper, nickel, and tin. The specific design of the strip depends on the design of the part needed. In some cases, the precious metal content of the manufactured component can be as low as 5%. With most of the parts being made from a more economical alloy, material cost is dramatically reduced while critical performance characteristics are maintained.
How is Bimetallic Strip Made?
Manufacturing bimetallic strips involves several tightly controlled steps:
- The precious metal strip is manufactured.
- The non-precious metal strip is manufactured.
- In a continuous process, the two strips are brought along an edge and joined by welding to make the bimetallic strip
- The bimetallic strip is then annealed and rolled several times until the desired thickness is achieved. The strip is then slit to the desired width.
The strip is now ready to be precision-stamped with specialty tooling that creates the component with optimized placement of the precious metal. Parts may then be heat treated to achieve the required physical properties i.e. stiffness to achieve a targeted contact force, and hardness to maximize resistance to sliding wear.
Applications
Contacts made from bimetallic strip are used in many applications where accurate position-sensing is required. Two common applications in the automotive market are throttle body position sensors and pedal position sensors.
In industrial, aerospace, and medical applications, these bimetallic contacts are also used extensively in position sensors and potentiometric devices where accurate signal transmission, reliability, and durability are required.
Limitations
Not all applications can take advantage of bimetallic components. Environments that cause copper-based alloys to corrode for example, would require a different approach such as solid precious metal or corrosion-resistant plating. In critical applications in corrosive environments monolithic precious metal components are typically used.
Conclusion
For manufacturers facing the persistent challenge of increasing precious metal costs, bimetallic strip represents an opportunity to optimize component design and reduce cost without compromising performance. While not a universal solution, this approach provides tremendous value across many industries. For applications that qualify, the combination of performance, reliability, and cost efficiency makes bimetallic strip technology the best choice.
Interested in learning if your contacts and budget can benefit from bimetallic strip? Contact us today so you we can review your application!