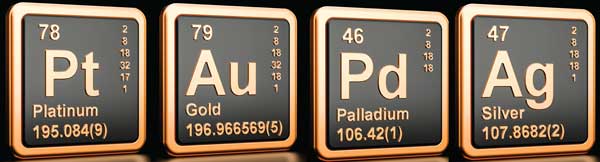
If something costs more, it’s better, right? It’s a simple rule we’ve all learned – higher price equals higher quality. Luxury cars, designer clothing, gourmet meals – the more expensive option typically promises better performance. But when it comes to material selection for components such as electrical contacts, this is simply not the case. The most expensive alloy isn’t always the best solution.
Manufacturers and engineers face a far more nuanced challenge when selecting electrical contact materials. Choosing the right alloy requires an understanding of performance characteristics that go beyond the price tag. It demands a strategic approach that balances electrical properties, mechanical durability, thermal management, environmental resilience, and more.
Electrical Properties
Let’s start with the most obvious aspect: electrical performance. Voltage and current requirements dictate the fundamental characteristics of the contact material. Different applications demand unique electrical properties, making it crucial to match the alloy precisely to the specific electrical demands of the system. Let’s see how each of the main categories performs:
- Gold Alloys – excel in low-voltage, precision electronic applications, offering exceptional oxidation resistance and electrical performance. They are ideal for more demanding uses such as medical devices and telecommunications, though their soft nature limits mechanical durability.
- Silver Alloys – are versatile performers in high conductivity, and arcing contacts, making them suitable for medium voltage applications across automotive, control, and certain industrial switching uses. They effectively handle moderate current loads while providing reliable electrical connection and interruption.
- Copper-Tungsten Alloys – are engineered for high-voltage and high-current environments, delivering excellent thermal management and mechanical durability. These alloys excel in demanding industrial switching applications where electrical stress and environmental resilience are critical performance requirements.
Conductivity vs. Nobility
Conductivity and nobility represent a critical trade-off in material selection. To illustrate this, let’s look at a few materials. Pure copper is considerably less expensive than gold and provides 100% conductivity. However, the low-price tag comes with a considerable drawback: it quickly oxidizes and then becomes ineffective. Conversely, noble metals like gold naturally provide exceptional resistance to oxidation, but at a significant cost. These are the extremes, and in the middle, there are options such as copper alloys or others such as nickel-plated steel. The goal is to identify the material that delivers the balance of conductivity and corrosion resistance for the specific application.
Operational Mechanics
Electrical contacts operate under two primary principles: wiping and sliding and make and break. Let’s look at each:
- Wiping and Sliding – this approach creates a self-cleaning action that removes surface oxides and debris as the contacts slightly rub against each other. This helps ensure a clean, low-resistance electrical connection. It also delivers consistent electrical performance over many cycles.
Wiping and sliding contact mechanisms are well served by noble metal alloys of gold, palladium, or platinum. These materials excel in low-voltage, precision applications where surface stability and oxidation resistance are critical. By creating a micro-abrasive motion during electrical connection, these alloys effectively remove surface contaminants, ensuring consistent low-resistance electrical performance. Typically employed in sensitive electronics, telecommunications, and medical devices, wiping and sliding contacts prioritize clean, reliable connections through controlled surface interaction. - Make and Break – determines the contact’s ability to establish and interrupt electrical connections. “Make” refers to the moment the contacts first connect, while “break” describes the instant the connection is disrupted.
Make and break contact mechanisms primarily utilize silver-based and copper alloys designed to handle high-voltage and high-current electrical switching. Silver and its composites, including silver-cadmium oxide and silver-tungsten, are particularly effective at managing electrical arcing and maintaining performance across repeated connection and disconnection cycles. These materials are engineered to withstand significant electrical stress, making them ideal for power switching, circuit breakers, and industrial electrical systems where rapid, reliable electrical interruption is required. The selection of make and break contact materials depends on specific voltage requirements, current load, switching frequency, and environmental conditions.
Hardness
Knoop Microhardness is another critical factor in contact material selection. Harder materials like Paliney or Palladium alloys offer superior resistance to deformation, ensuring consistent performance and longer contact life. This prevents unwanted distortion and maintains electrical reliability.
Thermal Management
Heat transfer and conductivity are also important considerations. The material must efficiently dissipate heat generated during electrical contact via sufficient thermal conductivity, while maintaining consistent performance across temperature variations. Performance should consider the maximum service temperature together with the coefficient of resistance (TCR) for the alloy. The selected material must also meet the thermal stability requirements of the specific application, particularly with regards to stress relaxation.
Environmental Challenges
Various operating environments present unique challenges. These include temperature fluctuations, humidity exposure, exposure to salt and chemicals, as well as debris and contamination. We could easily write a separate blog on this topic alone! The general approach though is to first make sure you fully understand the potential environmental threats for the contacts. Then match the needs with the properties of each material under consideration. Be sure to design for the extremes such as minimum or maximum temperature or amount of salinity. In doing so, you’ll reduce the likelihood of premature failure.
Conclusion
Material selection for electrical contacts is a complex process and requires consideration of many factors, as detailed above. By carefully evaluating electrical properties, operational mechanics, thermal characteristics, and environmental challenges, manufacturers can select materials that deliver optimal performance without unnecessary additional cost.
The right alloy is not the most expensive, but the one precisely engineered for your specific application.
Need assistance selecting the best alloy for your electrical contacts? Reach out to us today – we’re happy to help!