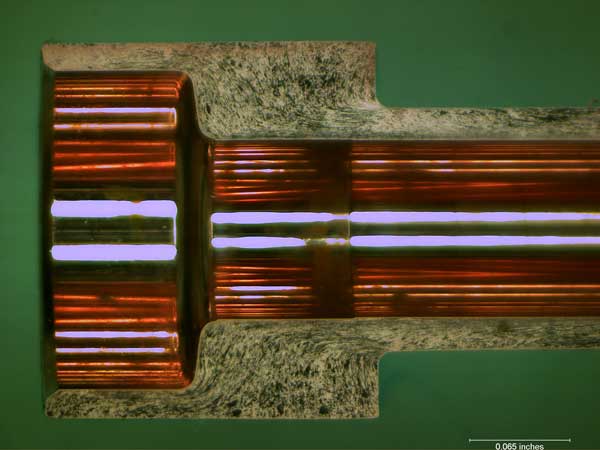
It’s generally understood that cold heading is an effective way to produce strong metal parts. This leads to a great question: what characteristics of this process give the final components such remarkable strength and performance? The answer lies in understanding the science behind cold heading. Let’s dive in.
Graded microstructures form the base of cold heading; these are structures made in the process that are basically not uniform. Since the metal is compelled to plastically deform and flow into the desired shape, it undergoes huge variations in crystal structure during the process. Consequently, regions under severe deformation turn significantly work-hardened and develop a refined grain structure with strength.
Let us now look at the key production parameters that are contributing to this hardening effect and the resulting graded microstructure.
Strain Magnitude – The process of cold heading usually consists of several forming sequences: for the cylindrical metal slug to obtain final part form, anywhere from one to six separate operations may occur. That is, with each successive “hit”, material strain increases cumulatively. Such successive or incremental deformation produces and multiplies dislocations within the crystal lattice of the metal; thus, work hardening ensues.
Interestingly, the extent of work hardening depends on the base material. Pure metals are hardened at relatively lower rates compared to alloys, because in the case of the latter, solid solution or precipitation strengthening elements are added which make dislocation movement through the lattice difficult and thereby increase the rate of work hardening.
Temperature – Unlike hot forming processes such as forging or extrusion, cold heading is done at room temperature, which prevents dynamic recrystallization at an elevated temperature and softening of the material. The cold deformation merely refines the microstructure by increasing the strength and hardness and reducing ductility.
The temperatures being fairly low for the process in concern provide minimal adiabatic heating and frictional heating effects, allowing the thermal consequence on the metal to be reasonably mild and maintaining the intrinsic properties of the starting material.
Strain Rate – Cold heading equipment is typically designed to operate at high volume, high speed. This results in extremely short times of deformation, on the order of fractions of a second per forming “hit.” The rapid nature of this process leads to very high strain rates that further contribute to work hardening.
This will become increasingly important when dealing with exotic or unfamiliar alloys. Materials that exhibit a low strain rate sensitivity will typically accommodate the large strain magnitudes associated with cold heading much better than those alloys that are more sensitive.
Examples of components enhanced by this process include, but are not limited to:
- Fasteners such as bolts, screws, and rivets
- Springs and other suspension components
- Precision instruments and medical devices
Cold heading draws much of its strength from the fundamental science involved in work hardening its material of choice through strategic plastic deformation. Cold heading represents a potent manufacturing process that continues to push the boundaries of what is possible with metal components.
Can your parts benefit from the strength that cold heading provides? Contact us to find out.