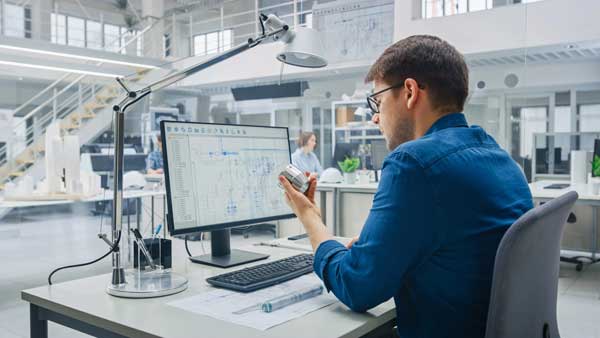
In today’s highly competitive market, manufacturers are constantly seeking ways to reduce costs without compromising quality. One effective approach that has gained traction over recent years is Value Analysis Value Engineering (VAVE or VA/VE). Here, suppliers and buyers achieve cost-cutting measures by collaborating to optimize products, requirements, and processes. Today, we’ll take a closer look at VAVE, what it is and what it isn’t, as well as specific areas where cost cutting can be realized.
What is VAVE?
VAVE is a systematic approach that aims to reduce costs without affecting the components function or reliability. But it’s more than a cost reduction method: it’s about enhancing value through innovation, efficiency, and optimization. VAVE is a collaborative process that involves analyzing the entire product lifecycle, from design to manufacturing to delivery, with the goal of maximizing value for all involved, right up to the end user.
What VAVE is NOT
It’s important to distinguish VAVE from other efficiency-driven processes such as Design for Manufacturability (DFM). While DFM focuses on designing products that are easier to manufacture, VAVE takes a broader approach. VAVE is not simply about blind price reductions or forcing suppliers to cut corners. Instead, VAVE is a holistic strategy that considers materials, processes, design, and supplier relationships to create value.
How is VAVE Achieved?
There are multiple aspects to successfully executing a VAVE program. Here at Deringer Ney, implementation relies on a few key aspects including material selection, process optimization and design enhancements. In some cases, logistics and packaging can contribute to program success as well. All programs do rely on collaboration, as we mentioned earlier. But this aspect can’t be understated, as ultimately, the customer must agree to changes recommended by the manufacturer prior to executing them. Let’s take a closer look at the “primary levers”:
Material Selection – here, engineers will carefully analyze materials used in production, often recommending alternatives that offer similar performance at a lower cost. For example, at Deringer Ney, our team might suggest using lower-cost alloys or reducing the amount of precious metals used in electrical contacts.
Process Optimization – By examining manufacturing processes, VAVE can identify more efficient production methods. For instance, this might involve switching from machining to stamping or cold forming. This could dramatically increase production rates while reducing cost. Switching to cold forming alone could bring significant part cost reductions for those that qualify. For larger piece runs, automation could be employed to significantly increase output, while preserving, and in some cases even increasing the quality and consistency of the components being produced.
Design Refinement – VAVE encourages designing features that work as intended without overengineering. This could mean reducing the amount of material used or simplifying complex components without compromising functionality. This is not always possible, depending on the part, its material and its use. But sometimes small changes in a component’s geometry can add up to bigger savings, especially if a process step can be either removed or simplified.
Logistics and Packaging – often overlooked, optimizing packaging and shipping can lead to measurable cost savings. This includes specifying economical shipping quantities and designing efficient packaging.
The VAVE Process
Implementing VAVE typically unfolds as follows:
- Analysis – The process begins with a thorough analysis of the product, its components, materials, and manufacturing processes.
- Ideation – Teams brainstorm potential improvements, drawing on their expertise in materials, processes, and design, along with VAVE experience with similar products.
- Evaluation – Ideas are evaluated for feasibility, potential cost savings, and impact on product performance.
- Testing – Promising ideas are tested and validated to ensure they meet all requirements.
- Customer Approval – keeping in mind that this is a highly collaborative process, nothing is changing without customer approval. While this often involved several parties/teams on the buyer’s end, having patience almost always pays off in the end.
- Implementation – Successfully validated improvements are implemented into the production process.
- “Rinse and Repeat” – VAVE is not a “one and done” effort! It is an ongoing continuous improvement process, with teams constantly exploring new optimization opportunities.
Challenges and Considerations
While VAVE offers many benefits, it’s certainly not without challenges. We already mentioned one of the biggest potential setbacks: it can be time-consuming, especially for parts already in production. Further, VAVE is not a one-size-fits-all solution. The potential for improvement varies depending on the part, its current design, and other factors we previously mentioned. Sometimes, the savings might be minimal, while in other cases, VAVE could lead to dramatic cost reductions.
Conclusion
Value Analysis Value Engineering is more than just a cost-cutting exercise; it’s a comprehensive approach to creating value in manufacturing. By encouraging collaboration and innovation, while focusing on holistic optimization, VAVE helps manufacturers stay competitive in an increasingly challenging market. As the industrial world continues to evolve, VAVE will play a crucial role in the future.